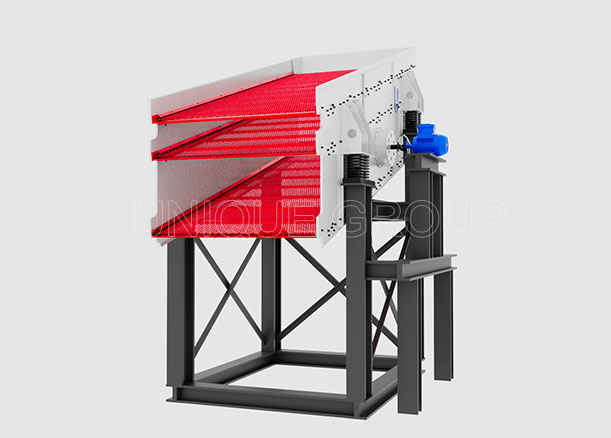
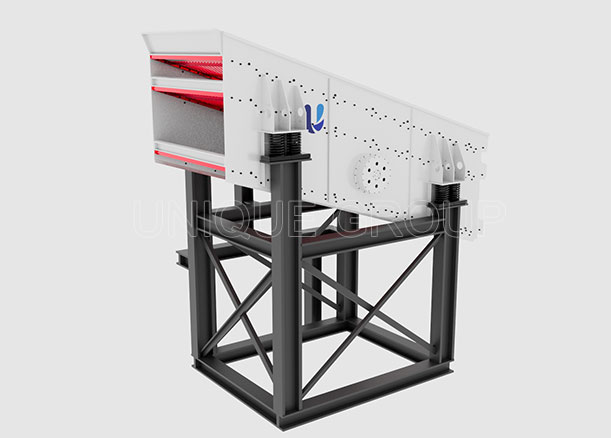
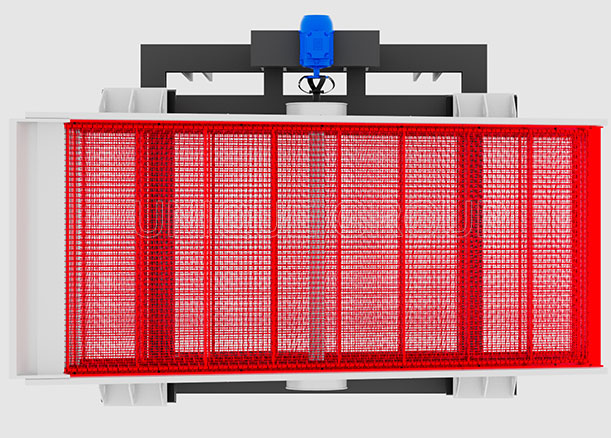
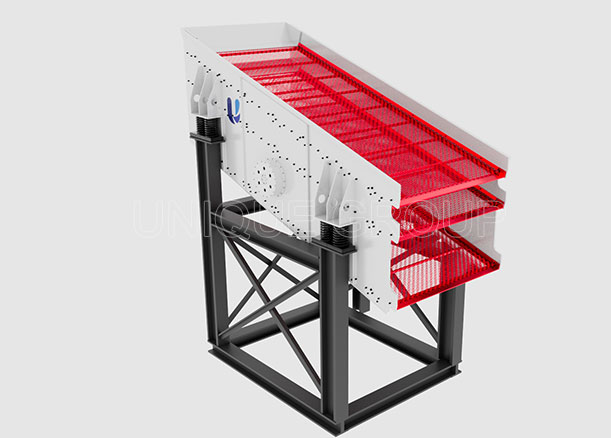
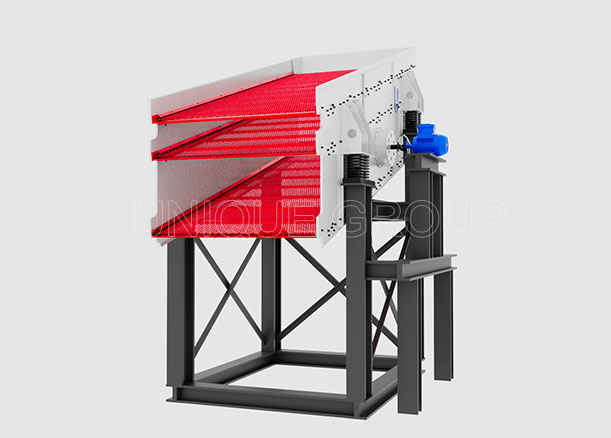
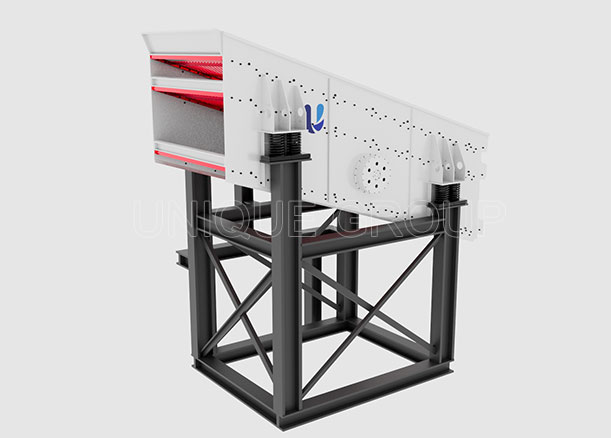
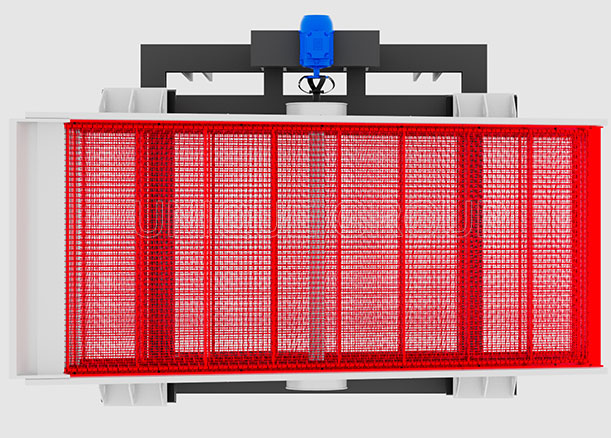
Vibrating Screen
Introduction:Circular Vibrating Screen is widely used for grading and screening materials in the fields of minerals, quarry, building materials, etc. Our vibrating screen has multi-layers and its screen size is various, it can screen out many kind of materials with different sizes.
What is the machine?: Inquiry Now
What is vibrating screen?
Vibrating screen is an important industrial screening equipment, widely used in mining, coal, chemical industry, building materials, food and other industries. The following is a detailed introduction to the vibrating screen from the aspects of definition, working principle, classification, application field and technical characteristics.
1. Definition of vibrating screenVibrating screen is a screening machine that uses the principle of vibration to classify, wash, dehydrate, and remove materials. Its main function is to separate the material on the screen through vibration, so as to obtain the screen material and the screen material of different particle sizes.
2. Working principle of vibrating screenThe core principle of vibrating screen is to generate vibration through a vibrating motor or other excitation device to make the material move on the screen, so as to achieve screening. The specific working process is as follows:
Vibration source: Vibrating motor or other excitation device provides vibration force.
Screening process: The material enters the screening machine evenly from the feed port, is separated through multiple layers of screens, and materials of different particle sizes are discharged from their respective outlets.
Movement mode: According to the different vibration modes, the vibrating screen can be divided into linear vibrating screen and circular vibrating screen. Linear vibrating screens make materials move along a straight line, while circular vibrating screens make materials move along a circular trajectory.
3. Classification of vibrating screensAccording to the vibration trajectory, purpose and excitation method, vibrating screens can be divided into the following categories:
Linear vibrating screen: The vibration trajectory is a straight line, with high screening efficiency, suitable for mining, coal, building materials and other industries.
Circular vibrating screen: The vibration trajectory is circular, with high screening accuracy, suitable for chemical, food and other industries.
Elliptical vibrating screen: Combining the characteristics of linear and circular vibrating screens, it is suitable for screening special materials.
4. Application fields of vibrating screensVibrating screens are widely used in the following fields due to their high efficiency and stability:
Mines: used for ore grading and mineral processing.
Coal: grading, de-mediuming and dehydration of coal.
Chemical industry: used for screening and grading of chemical raw materials.
Building materials: screening of materials such as cement and glass.
Food: used for grading and screening of food raw materials.
5. Technical features of vibrating screenVibrating screen has the following technical advantages:
High-efficiency screening: rapid material separation through vibration.
Strong adaptability: can handle a variety of materials and particle size ranges.
Low noise, low energy consumption: optimized design, smooth operation.
Easy to maintain: simple structure, easy maintenance.
Summary
As an efficient and stable screening equipment, vibrating screen plays an important role in many industries. It generates vibration force through a vibrating motor to achieve material classification and separation, and is widely used in mining, coal, chemical and other fields. According to the different vibration trajectories and uses, vibrating screens can be divided into linear vibrating screens, circular vibrating screens and other types, each type has unique characteristics and advantages.
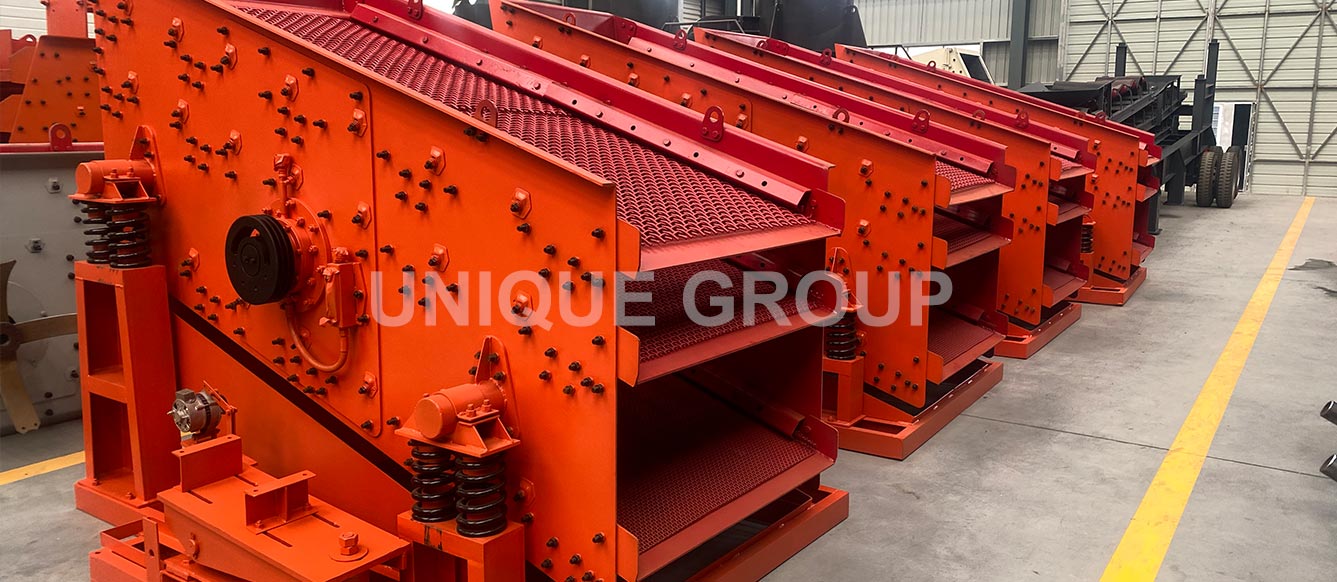
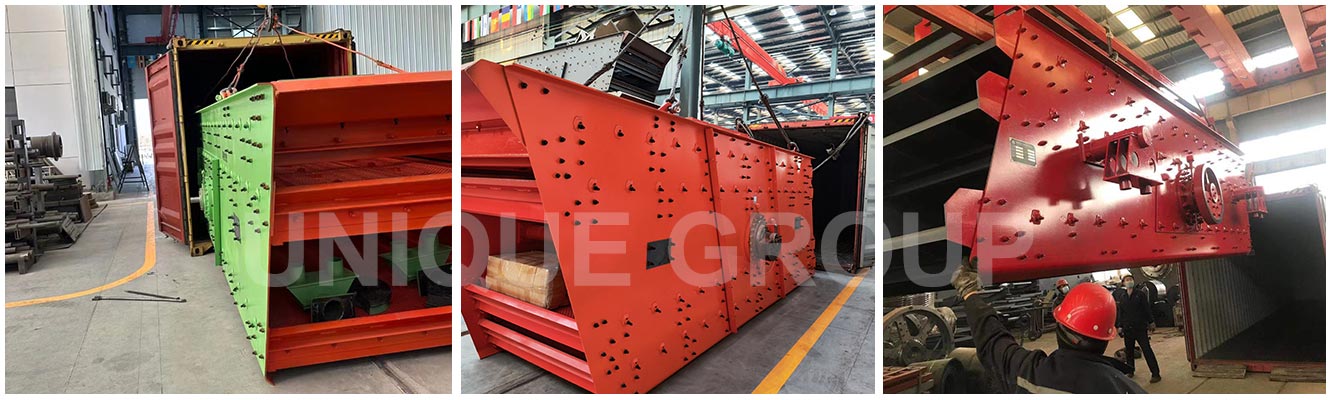
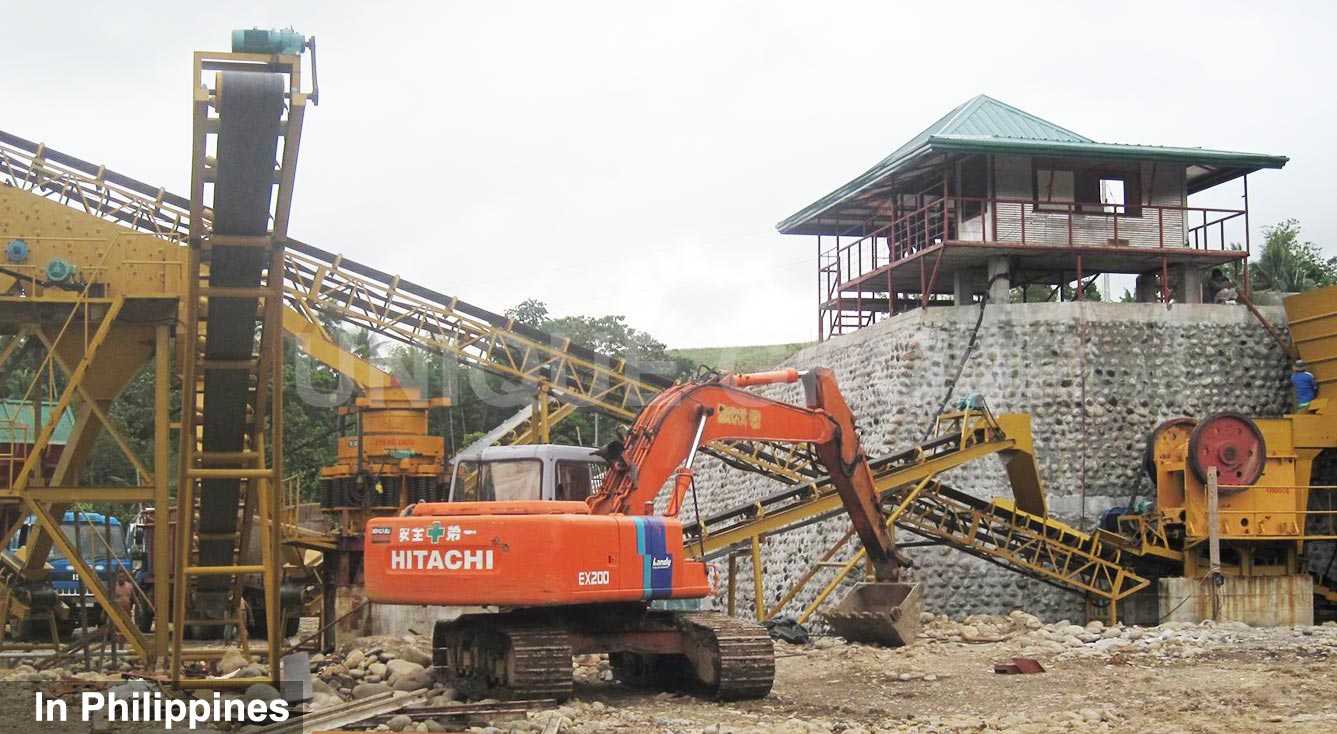
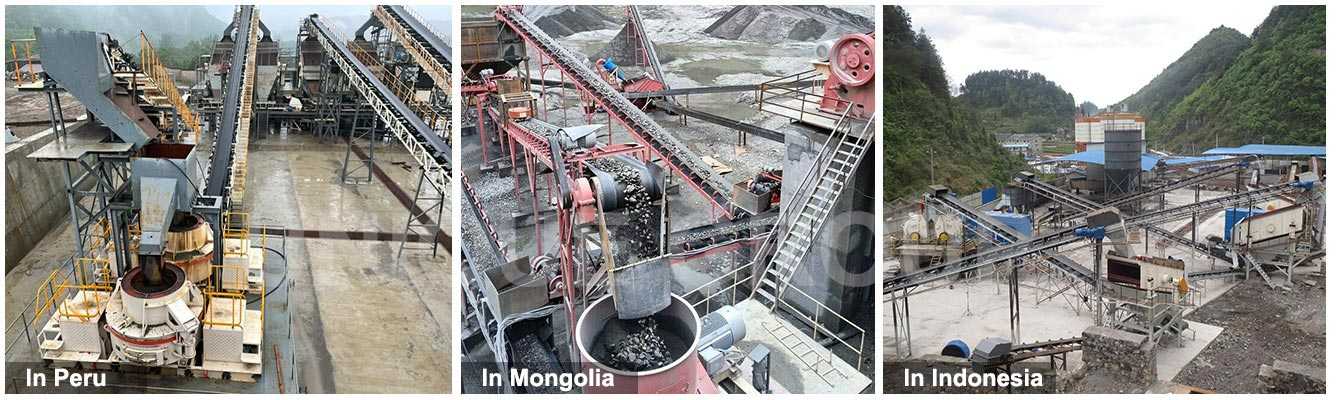
How does it works?: Inquiry Now
Working principle of mining vibrating screen
Mining vibrating screen (Vibrating Screen) is a screening equipment that classifies materials by particle size through vibration. It is widely used in ore crushing, sand making, mineral processing and other processes to ensure that the finished product particle size meets production requirements.
1. Working process of vibrating screen
a.Vibration source start:
The vibration motor (or exciter) generates high-frequency vibration force to drive the screen box and screen to vibrate.
Common vibration source types:
Dual vibration motor: The two motors rotate in opposite directions to produce a linear or elliptical vibration trajectory.
Eccentric block exciter: Centrifugal force is generated by the rotation of the eccentric block to form a circular vibration.
b.Material stratification and screening:
After the material enters the screen surface from the feed inlet, under the action of vibration:
Stratification: Large particles float up, and small particles sink to the surface of the screen.
Screening: Particles smaller than the size of the screen hole fall through the screen into the lower screen or the collecting hopper.
Unscreened material: Moves along the screen surface to the discharge end and is output as coarse material.
c.Multi-stage screening (taking multi-layer screen as an example):
The screens are arranged in layers from large to small according to the aperture (such as 10mm on the upper layer, 5mm on the middle layer, and 3mm on the lower layer).
The materials are screened layer by layer, and finally a variety of finished products (such as coarse sand, medium sand, and fine sand) are output.
2. Core technical points of vibrating screen
a.Vibration mode and trajectory:
Linear vibration: suitable for rapid screening of dry materials (such as sand, gravel, and coal).
Elliptical vibration: taking into account both conveying speed and screening accuracy (such as wet and sticky materials).
High-frequency vibration: used for efficient classification of fine-grained materials (such as slurry and powder).
b.Screen structure optimization:
Material: high manganese steel, polyurethane or rubber screen, adapted to different material characteristics (wear resistance/anti-blocking).
Tensioning method: bolt fixing or spring tensioning to ensure the flatness of the screen and reduce material jamming.
c.Shock absorption and stability:
Use rubber springs or spiral springs to support the screen body to reduce vibration transmission to the foundation.
Dynamic balance design avoids structural damage to the screen due to partial load.
Solutions: Inquiry Now
Model | Sieve Layer | Mesh Size(mm) | Max. Feeding Size(mm) | Capacity (m³/h) | Motor Power(kw) | Weight(kg) |
2YK1225 | 2 | 4-50 | 400 | 8-60 | 5.5 | 2500 |
3YK1225 | 3 | 4-50 | 400 | 10-70 | 5.5 | 2850 |
2YK1230 | 2 | 4-50 | 400 | 12-78 | 7.5 | 3000 |
3YK1230 | 3 | 4-50 | 400 | 13-80 | 7.5 | 3600 |
2YK1237 | 2 | 4-50 | 400 | 15-86 | 7.5 | 3600 |
3YK1237 | 3 | 4-50 | 400 | 16-90 | 7.5 | 4200 |
2YK1535 | 2 | 5-50 | 400 | 20-125 | 11 | 4890 |
3YK1535 | 3 | 5-50 | 400 | 21-125 | 11 | 5700 |
2YK1545 | 2 | 5-50 | 400 | 22-150 | 15 | 5330 |
3YK1545 | 3 | 5-50 | 400 | 22-150 | 15 | 5800 |
2YK1548 | 2 | 5-50 | 400 | 22.5-162 | 15 | 5980 |
3YK1548 | 3 | 5-50 | 400 | 22.5-162 | 15 | 6600 |
2YK1848 | 2 | 5-80 | 400 | 25-206 | 15 | 7080 |
3YK1848 | 3 | 5-80 | 400 | 32-276 | 18.5 | 7600 |
2YK1854 | 2 | 5-80 | 400 | 32-312 | 18.5 | 8150 |
3YK1854 | 3 | 5-80 | 400 | 32-312 | 22 | 8840 |
2YK2160 | 2 | 5-100 | 400 | 50-475 | 30 | 9780 |
3YK2160 | 3 | 5-100 | 400 | 50-475 | 30 | 10800 |
2YK2460 | 2 | 5-100 | 400 | 65-550 | 37 | 13600 |
3YK2460 | 3 | 5-100 | 400 | 70-620 | 37 | 15600 |
Typical application scenarios of vibrating screen
a.Applicable scenarios:
Mine crushing line: Screening of crushed stones, separation of qualified particle size and return material (such as jaw crusher + cone crusher + vibrating screen).
Sand making production line: Control the fineness modulus of finished sand (such as 3mm or less for machine-made sand, and 5mm or more for return to the sand making machine).
Ore dressing plant: Wet screening of slurry to separate useful minerals from waste rock.
b.Equipment selection reference:
Material type Recommended vibrating screen type Screening efficiency
Dry sand and gravel,coal Linear vibrating screen (ZK series) 90%-95%
Wet sticky slurry, fine powder High-frequency dewatering screen (DZS series) 80%-85%
Large ore pre-screening Heavy-duty circular vibrating screen (YA series) 85%-90%
c.Efficiency and environmental protection design:
Sealed dustproof: The screen box is covered with a dust cover and connected to the dust removal pipeline to reduce dust emission.
Water spraying and dust reduction: When screening sticky materials, a spray system is added to prevent the screen holes from being blocked.
Intelligent monitoring: Install vibration sensors and temperature probes to monitor the operating status of the equipment in real time.
IV. Precautions
Screen maintenance: Regularly clean up blocked objects, check screen wear, and replace damaged screen surfaces in time.
Vibration parameter adjustment: Adjust the vibration frequency and amplitude according to the material characteristics (humidity, viscosity).
Installation requirements: Ensure that the screen is placed horizontally and the foundation concrete strength meets the standard (above C25).
Application case:
An iron ore beneficiation plant uses 2YK3070 circular vibrating screen (double-layer screen, upper layer 10mm, lower layer 5mm), with a processing capacity of 300t/h, a screening efficiency of 92%, a return rate of 18%, and an annual power saving of about 80,000 kWh.
Summary:
The mining vibrating screen drives the material to be layered and screened through vibration to achieve precise particle size classification, and is the "quality gatekeeper" of the mining production line. Reasonable selection of vibration mode, screen configuration and maintenance plan can significantly improve production efficiency and resource utilization.