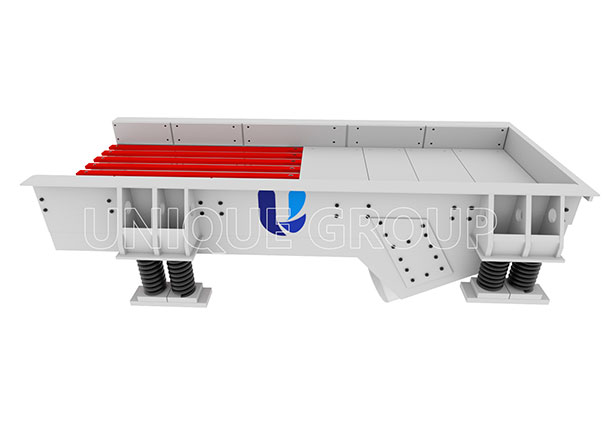

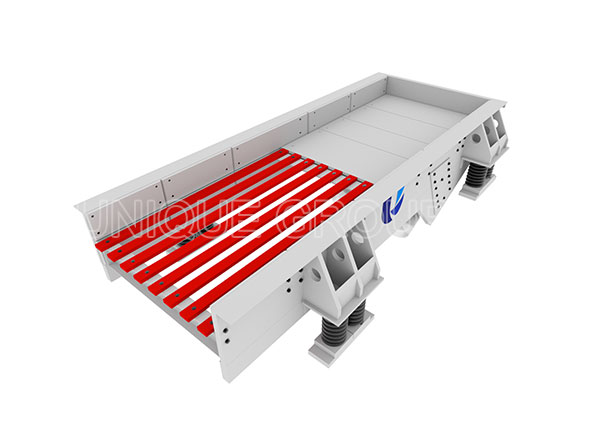
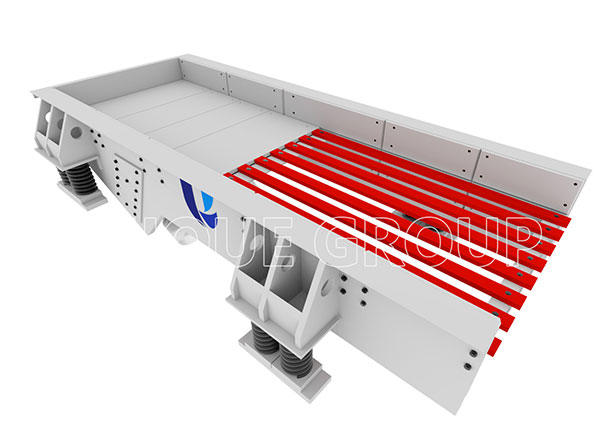
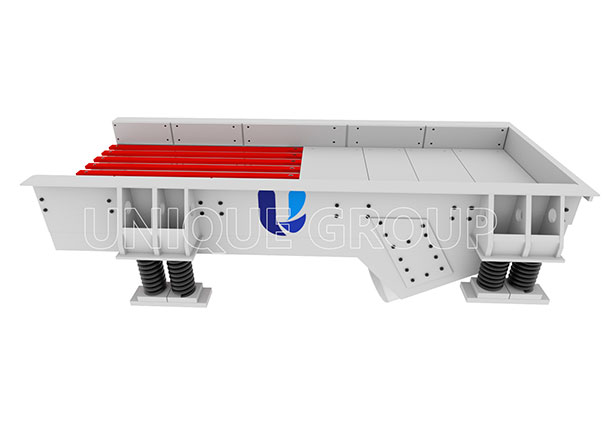

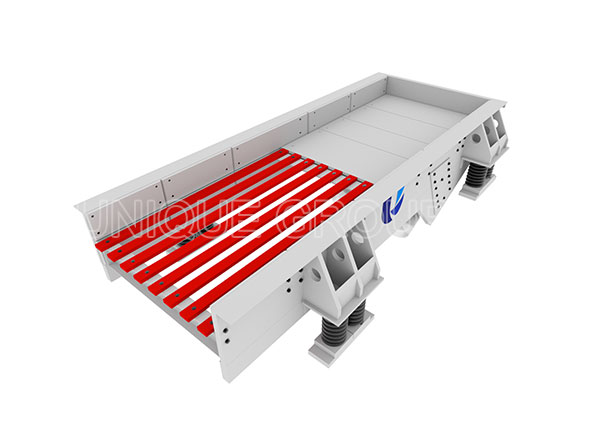
Vibrating Feeder
Introduction:Vibrating Feeder is a kind of linear direction feeding equipment. It can send shaped and granule materials into crusher evenly, timely and continuously as well as screen the materials roughly. The vibrating feeder is widely used in crushing and sieving production line such as metallurgy, building material, chemical industry, coal, mining and grinding industry.
What is the machine?: Inquiry Now
What is a mining vibrating feeder?
A mining vibrating feeder (Vibrating Feeder) is a mining mechanical equipment that uses the principle of vibration to evenly and continuously transport materials to the next process. It is often used in the starting link of production lines such as crushing, screening, and sand making.
Core functions:
Uniform feeding: avoid material accumulation or material interruption, and protect subsequent equipment (such as jaw crusher) from impact.
Pre-screening: filter fine particles through the screen to improve the overall production line efficiency.
Wide applicability: can transport large pieces of ore, gravel, sand and wet sticky materials.
Common types:
Electromagnetic vibrating feeder: driven by an electromagnetic exciter, suitable for small production lines with precise control. Motor vibrating feeder (inertial type): powered by a vibrating motor, with a simple structure and easy maintenance, suitable for medium and large mines.
Heavy plate feeder: used for the transportation of super-large pieces of material (such as 1-2 meters of ore), with strong impact resistance.
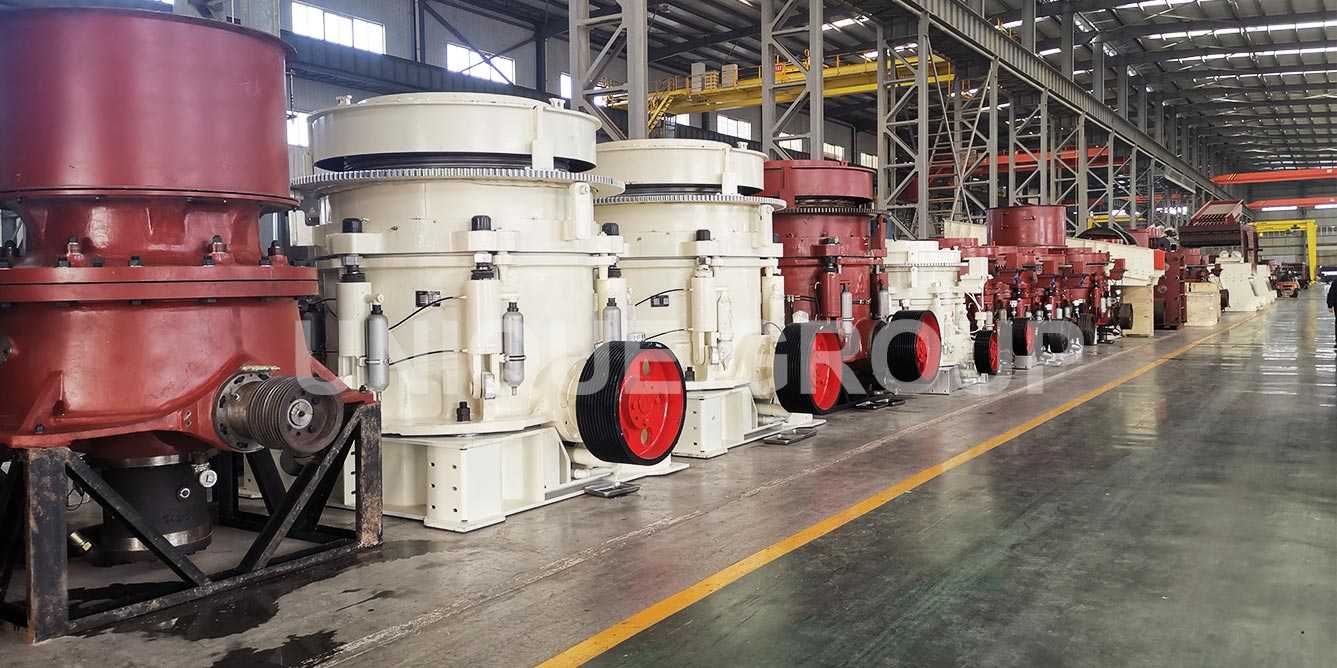
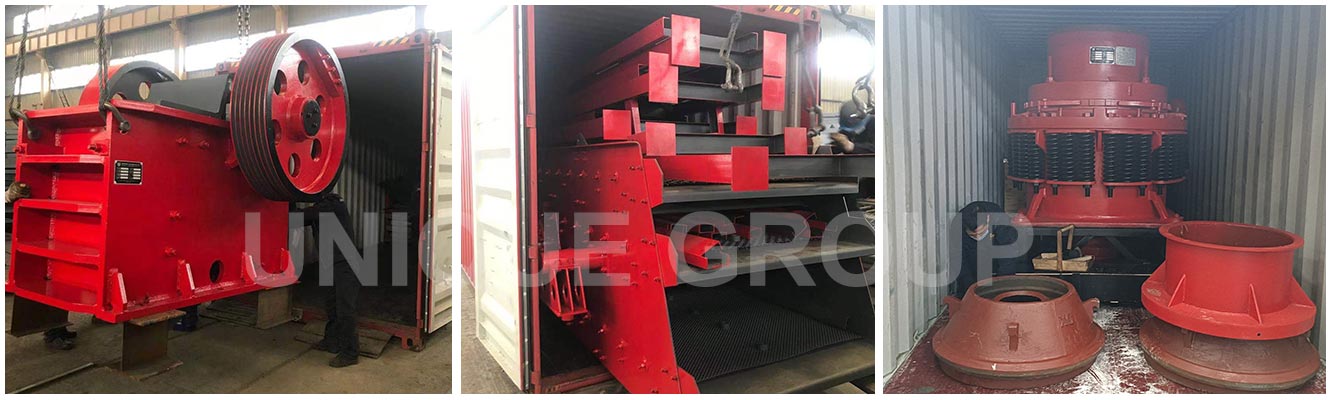
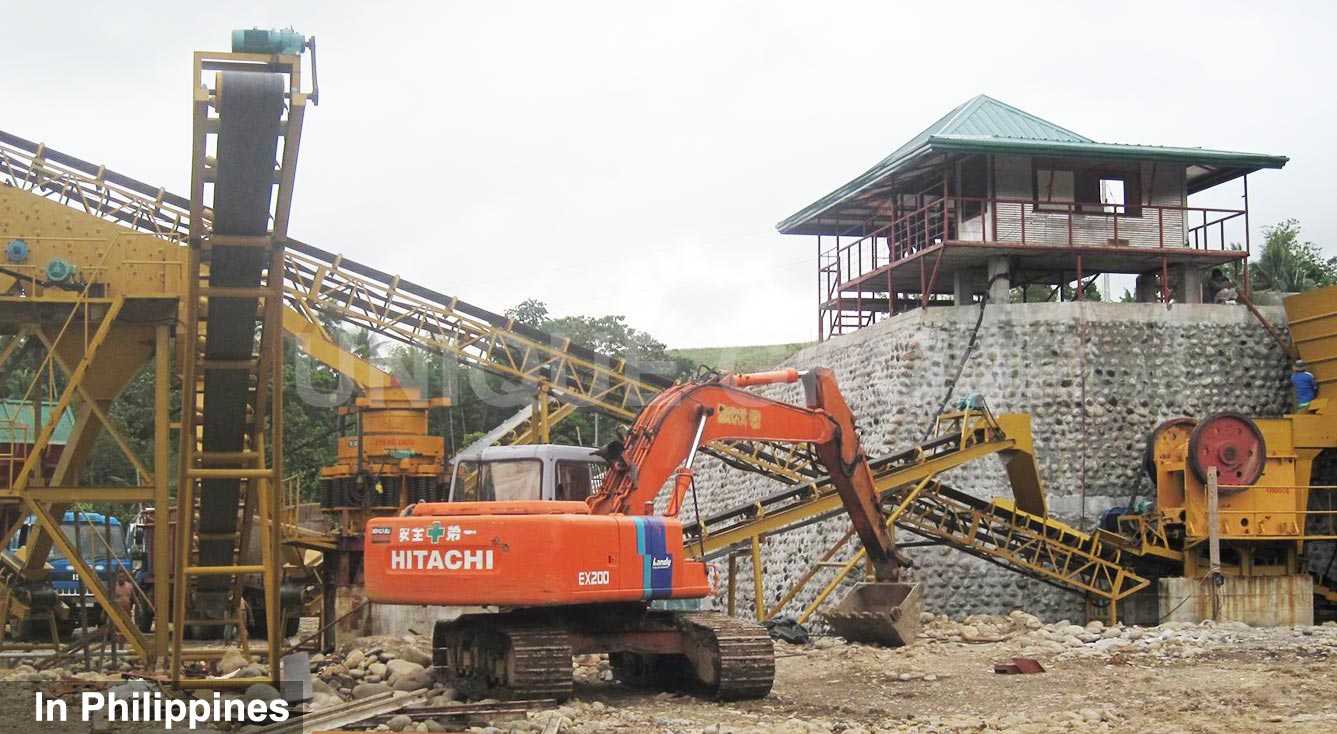
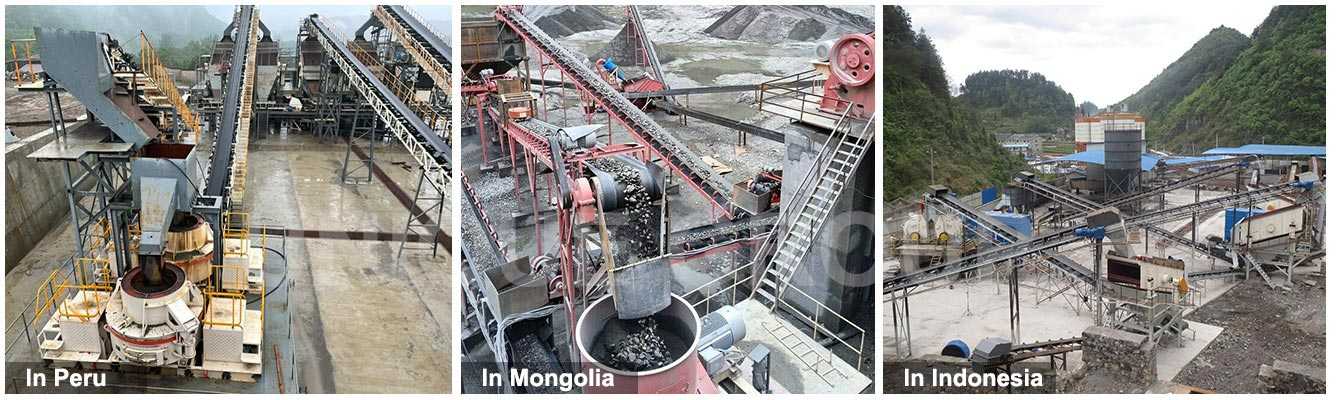
How does it works?: Inquiry Now
Working principle of vibrating feeder
Workflow (taking motor vibration type as an example):
Power source: Vibrating motor (dual motors are installed symmetrically) generates exciting force, which is transmitted to the feeding trough through springs or rubber shock absorbers.
Material conveying: The trough vibrates at a certain frequency and amplitude, and the material is thrown up and moves forward in a jumping manner under the action of inertia.
Flow control: By adjusting the angle or voltage of the motor eccentric block, the size of the exciting force is changed to control the feeding speed and flow.
Key technical points:
Dual motor self-synchronization technology: Ensure that the exciting force is superimposed when the two motors rotate in reverse to form directional vibration.
Shock absorption design: Use rubber springs or spiral springs to reduce the impact on the foundation.
Variable frequency speed regulation: Stepless speed regulation is achieved through the frequency converter to meet the needs of different working conditions.
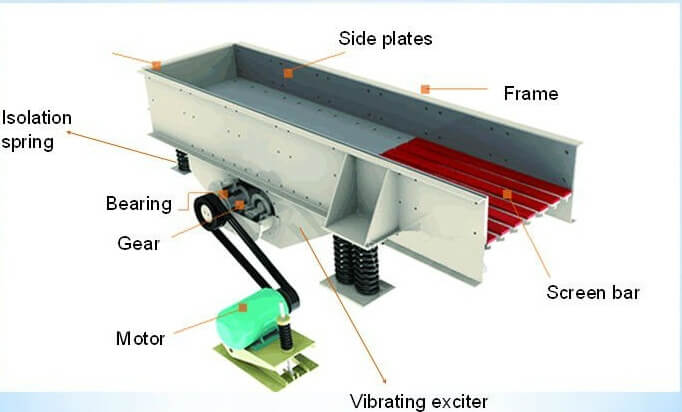
Solutions: Inquiry Now
Application scheme of vibrating feeder
1. Applicable scenarios
Mining crushing line: Feed evenly to jaw crushers, cone crushers, etc. to avoid equipment overload.
Sand production line: cooperate with sand making machine to stably transport stone materials and ensure uniform particle size of finished sand.
Ore dressing plant: used for initial screening of ore, separation of soil and debris, and improvement of ore dressing efficiency.
Coal industry: transport raw coal to coal washing equipment to reduce the risk of blockage.
2. Typical configuration scheme
Material type: granite, iron ore, coal, construction waste, etc. (particle size ≤1000mm).
Equipment selection:
Small production line: electromagnetic vibrating feeder (power 0.5-3kW, processing capacity 10-100t/h).
Medium and large mines: motor vibrating feeder (power 5-15kW, processing capacity 200-1000t/h).
Extra large mines: heavy plate feeder (processing capacity up to 2000t/h).
Intelligent upgrade: add sensors to monitor vibration amplitude and motor temperature in real time, and connect to the central control system.
3. Efficiency and environmental protection solutions
Sealing design: Install a dust cover above the tank body, and cooperate with dust removal equipment to reduce dust spillage.
Wear-resistant lining: For high-hardness ores (such as quartzite), the tank body is lined with manganese steel plates to extend the service life.
Energy-saving mode: Adopt variable frequency drive, automatically reduce frequency when unloaded, and save energy by 20%-40%.
IV. Precautions
Installation requirements: Keep the feeder installed horizontally, with an inclination angle of ≤10° to avoid material deviation.
Daily maintenance: Regularly check the tightness of bolts, spring fatigue and motor bearing lubrication.
Material adaptability: Viscous materials need to reduce the vibration frequency to prevent blockage; wet materials can be equipped with a tank heating function.
Application case: An iron ore production line is equipped with a motor vibrating feeder (model GZD-1500×6000), with a processing capacity of 800t/h, a pre-screening soil removal rate of >30%, a crusher efficiency increase of 25%, and an annual power saving of 120,000 kWh.
Summary: Vibrating feeder is the "throat" equipment of the mine production line. Its stability and efficiency directly affect the overall production capacity. Reasonable selection and scientific maintenance can greatly reduce the risk of downtime and help mines achieve efficient and green production.